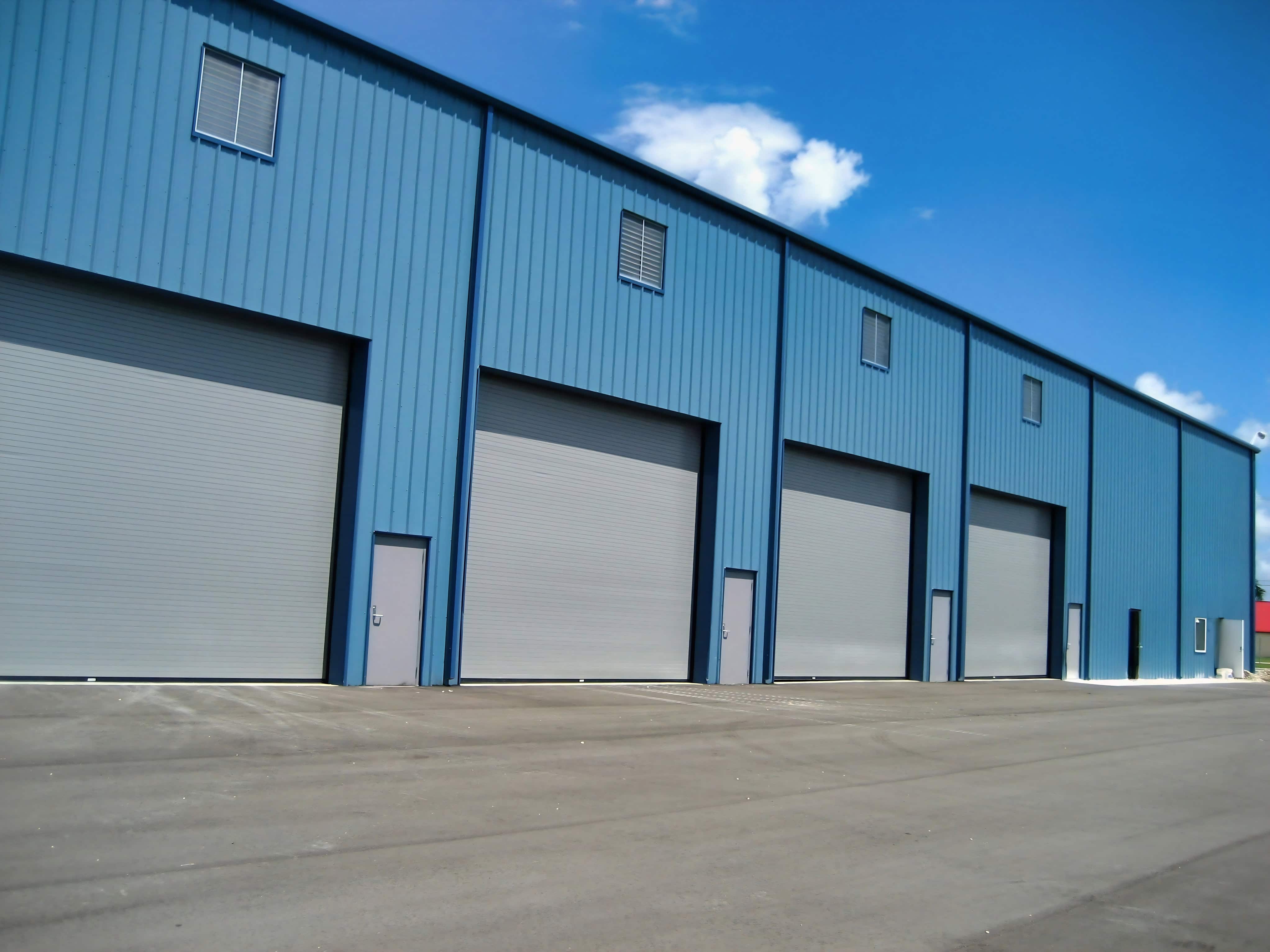
Metal Building Buyer’s Guide
This guide is our attempt to share our industry knowledge and practical experience with you in an effort to ensure that you don’t fall victim to some of the errors we have witnessed others make over the past 20 years.
With almost two decades in the steel building business, Buck Steel has accumulated a vast amount of experience serving a wide variety of customers in planning, designing, and erecting their metal building projects. Our pre-engineered metal building customers have taken us from The Florida Keys all the way to Washington State and countless places in between.
This Metal Building Buyers Guide is our attempt to share some or our industry knowledge and practical experience with you in an effort to ensure that you don’t fall victim to some of the errors we have witnessed others make over the years. If you are about to get started on your first metal building project, we hope you will take time to read this guide and call us if you have any questions.
While we certainly hope you will choose Buck Steel as your metal building supplier, irrespective of whom you choose, we want your project to be a successful and hope these tips on buying metal buildings will help get your project off on the right foot.
Building Departments & HOA’s
The first step in any metal building project is to check with your local building department to determine if they will even allow you to put up a metal building on your property. Some municipalities have restrictions on the use of steel buildings and some require the use of stucco, brick, or other exterior finishes on one or more sides of the building. Additionally, there might be size or height restrictions due to zoning and setback requirements.
It’s likely you are going to get quotes from multiple companies. Before making a purchase decision, visit your local building department with a copy of the quote from the company you are considering doing business with and get a preliminary verbal approval before proceeding.
Lastly, check with your HOA as it might have its own restrictions on the use of a steel building on your property. You do not want to have signed a Sales Contract and placed a deposit on your backyard shop, only to find out that your HOA is not going to allow you to put it up.
Anchor Bolt Plans
The difference between anchor bolt plans and foundations plans is often a source of confusion for many metal building customers. Anchor Bolt Plans come standard with all buildings and are provided by the metal building manufacturer. They are not a “separate” set of plans, but rather are usually page 2 or 3 of the full set of building plans.
Anchor bolt plans are simply drawings representing the design of the base plates on the columns, showing the location of the anchor bolts used to secure the building to the slab. In simple terms, they tell your concrete contractor where to place the anchor bolts when forming the piers for the project.
Anchor bolt plans also specify the diameter of the anchor bolts to be used but they do not specify the length of the anchor bolts. The length of the anchor bolts is specified by the Structural Engineer after the depth of the piers has been engineered.
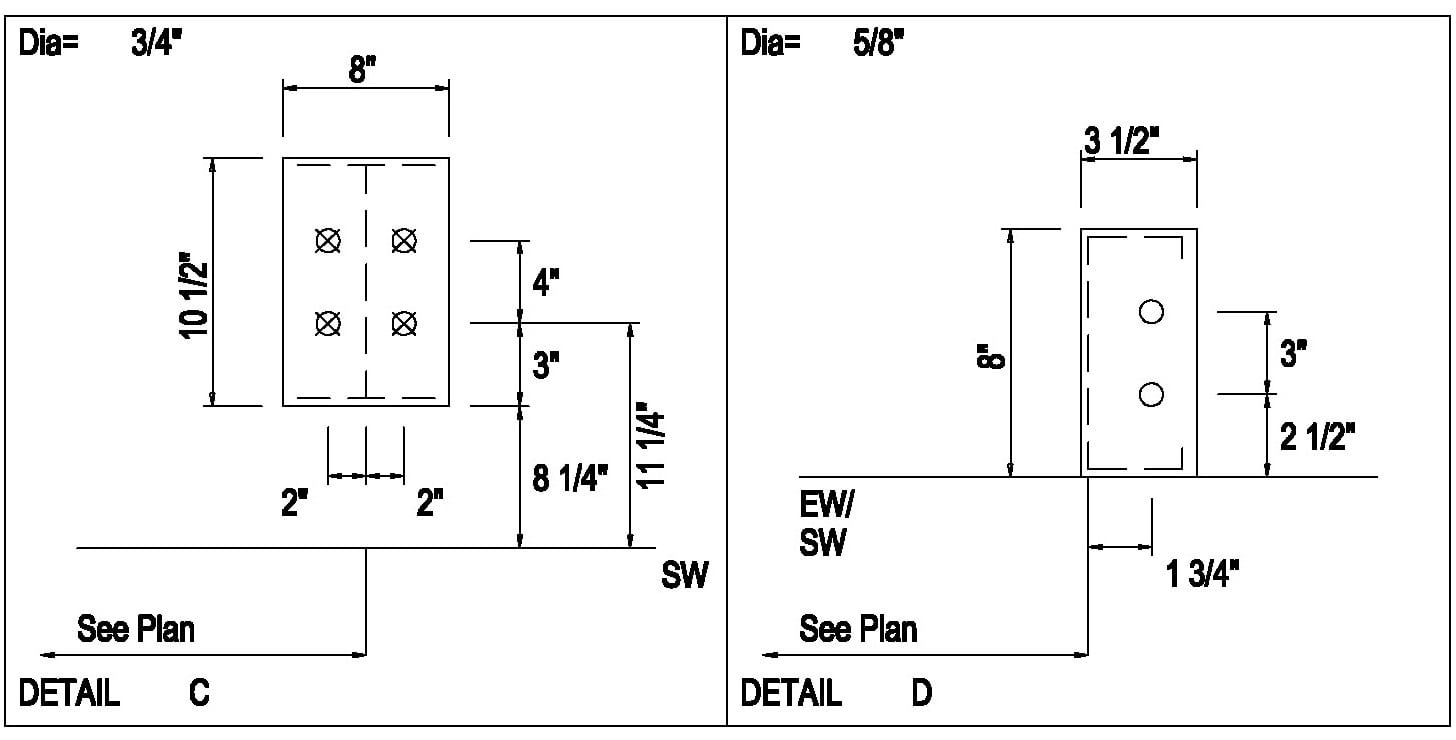
Foundation Plans
Foundation Plans are designed by a Structural Engineer licensed in your state. The Structural Engineer uses the building engineering along with the jobsite’s soil condition, seismic activity and other geological factors to engineer the size of the piers that will need to be poured under each of the columns of the building (as well as the size of the grade beam running around the perimeter of the building connecting the piers).
Foundation plans contain important information for your concrete contractor regarding the size and depth of the piers to be poured, size and placement of rebar, wire mesh, hairpins, and underlayment details. Foundation plans might also include loading dock or stem wall details.
Stamped engineered foundation plans work hand-in-hand with the building plans and are required as part of the permit process and to ensure a successful project.
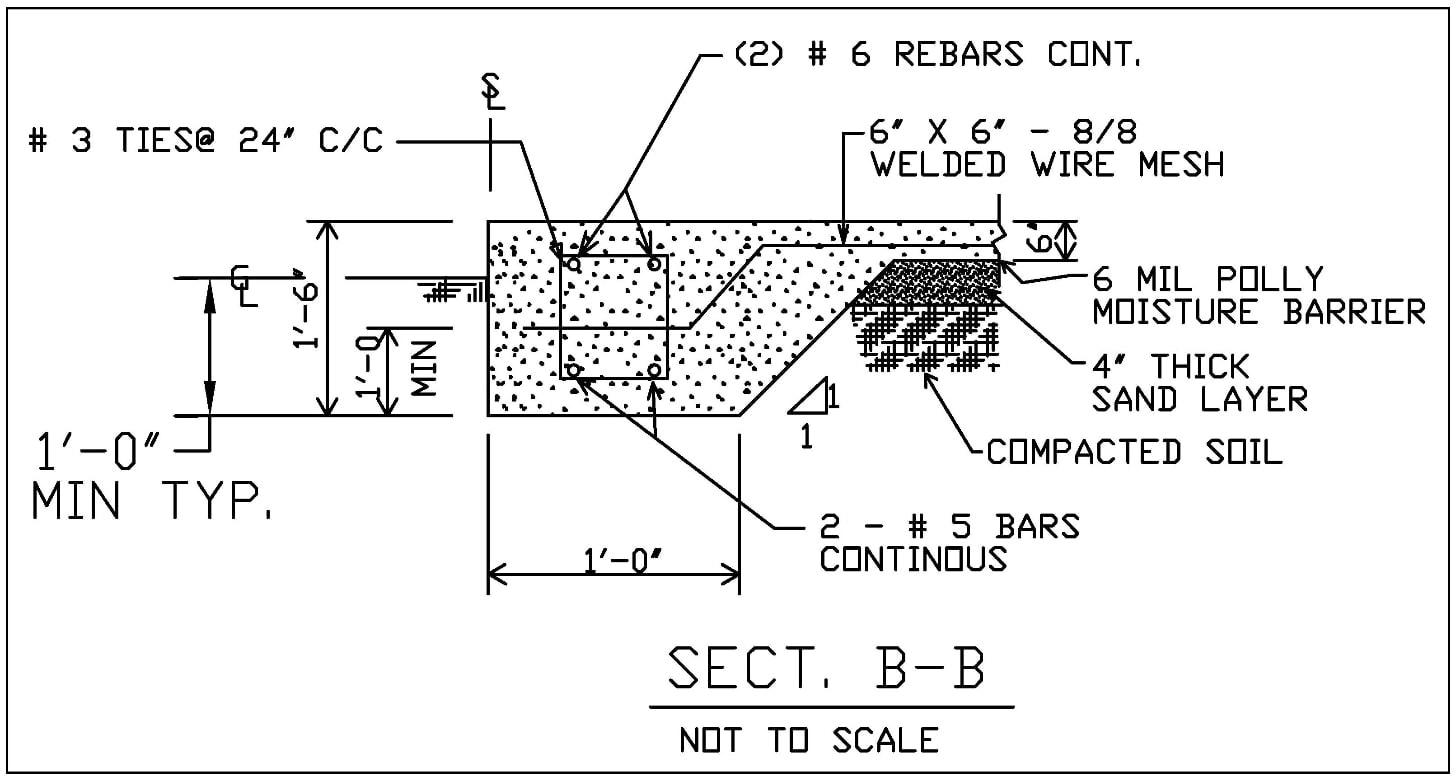
Wind Rated vs Wind Certified
Wind “rated” simply means that the door being provided for your metal building has been subjected to internal wind testing by the manufacturer of the door.
Wind “certified” means that the door being provided for your metal building has gone through very intense wind testing in an independent laboratory, meets all the requirements of the pressures required to sustain certain weather conditions, and will have a label stating such affixed to the door.
Whether or not you need a wind “rated” door, a wind “certified” door, or simply a standard door will depend on your local building department. The difference in price of a standard door and a wind “certified” door can be substantial!
Full Cover Trim vs Trim Package
Some companies use the term “trim package” to lead you to believe that you are getting a complete trim piece to cover the “C” channel framed opening – otherwise known as “full cover trim”, when in fact they are merely providing you with the basic “J-trim” package provided with every building.
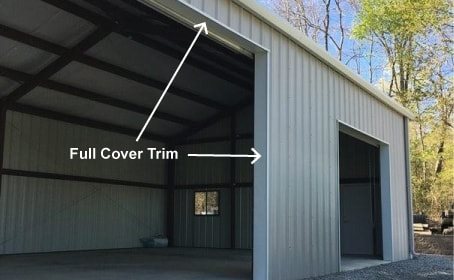
Some companies use the term “trim package” to lead you to believe that you are getting a complete trim piece to cover the “C” channel framed opening – otherwise known as “full cover trim”, when in fact they are merely providing you with the basic “J-trim” package provided with every building.
Comparing Quotes
If this is your first experience shopping a metal building, one of your most difficult tasks is going to be comparing quotes. Speaking honestly, comparing quotes is sometimes a bit of a challenge even for those of us in the business.
First, make sure that all of the quotes you have obtained are for the same kind of metal building. The term “metal building” gets thrown around pretty loosely to describe: tube steel buildings, cold form buildings, red-iron buildings, wood framed-metal sheeted buildings and even Quonset hut buildings. You have to make sure you are comparing quotes for the same kind of building in order to be fair to the suppliers quoting your project, as well as yourself.
Second, toss out any quotes provided to you by any metal building company telling you it’s a “one-day special offer” or “cancelled order”. Generally speaking, steel building companies that use the “cancelled order” pitch are often the least reputable in the business and simply telemarketing firms after a deposit (that you will likely never get back).
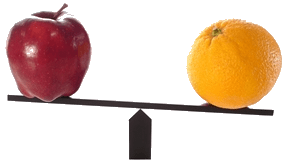
Third, discard any and all quotes that doe not clearly specify the engineering details used to design the building being quoted. Study the remaining quotes and attempt to compare apples with apples (a simple spreadsheet can be helpful here).
Make sure that the length, width, height, and roof pitch are the same. Also make sure the building code, wind load, wind exposure, live load, snow loads and other engineering details are all the same.
Differences in engineering details between quotes could result in a significant difference in price. Make certain that features you assume to be included are listed on your quotes as “included” and not listed in the “options” section or listed in a confusing or misleading manner. All included items and optional items should be clearly marked as such.
Remember, if it isn’t listed in writing as being included – then it isn’t. We regularly have customers send us in quotes from our competitors and are amazed at the misleading wording and techniques that are used to list items that are not included in the quoted price.
The Bump
Don’t let yourself fall victim to “The Bump”. Telemarketers and dishonest steel building companies will often price your building with wind, exposure, or snow load requirements LESS than your local building codes require just to quote you an artificially low price.
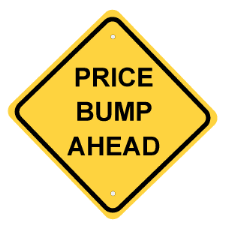
Once they obtain your non-refundable building deposit, they will advise you that the cost of your building is substantially higher than what was originally quoted due to modifications needed in order to meet your local building codes.
Once the change orders start coming your way to bring your building up to code, your “big deal” is going to turn into a big nightmare.
Accessory Placement
Accessory placement affects cost. Every metal building needs to be braced in order to maintain its structural integrity and to meet local codes/loads. Depending on the bracing method used, the bay being braced might be unavailable for use with accessories such as rollup doors, personnel doors, windows, etc. or an alternative higher cost bracing method might have to be used.
Be suspicious of any steel building company that does not discuss accessory placement prior to providing you a quote. Additionally, the placement of your accessories should be clearly specified on your quote – as well as the bracing method used to brace the steel building.
The Cancelled Order
The “cancelled order” pitch is the oldest trick in the metal building hustlers playbook.
While we have mentioned the infamous “cancelled order” sales pitch earlier it bears another mention. Beware of any steel building company that allows their salesmen to use this dishonest selling technique. The “cancelled order” sales pitch has been used by unethical salesmen, telemarketers, and untrained metal building brokers for ages. Why? Because it works! Unsuspecting customers fall for it all the time – everyone wants to think they are getting a “special” deal.
We recommend that if you hear about “one-day sales” or “cancelled orders” and are asked to provide a credit card number over the phone for a deposit that you hang up the phone! Find another company to work with and remember that the overwhelming majority of metal building companies are honest, knowledgeable, and eager to have your business.
The Buck Steel Advantage
Whether you are considering a 40′ x 60′ metal garage, a 10,000 sq. ft. steel warehouse, a 3,000 sq. ft. steel airplane hangar, a 30,000 sq. ft. open steel riding arena, or a new steel church for your congregation, a steel building project can sometimes be intimidating to navigate alone. Whether for personal or business use, you want to minimize the cost of your steel building project while maximizing the benefit it provides.
Why not give yourself The Buck Steel Advantage and have a reputable metal building supplier, serving the steel building customer for nearly 20 years, with 1,000’s of completed projects, guide you through the metal building process?
Getting started is easy with Buck Steel
Request A Quote Today or Call (866) 574-2825 to speak to a member of our team.
We welcome your comments and questions!